LP-0880 - Steel: The Problem of a Standardized Surface
Technical Bulletins
Posted 2023
Last Updated 2023
LP-0880
STEEL: The Problem of a Standardized Test Surface
If coatings tests are to be reliable and reproducible, they must be performed on a substrate which is reasonably consistent from test to test. Unfortunately, ordinary commercial sheet steel displays wide variations in the surface properties which affect the bonding of coatings.
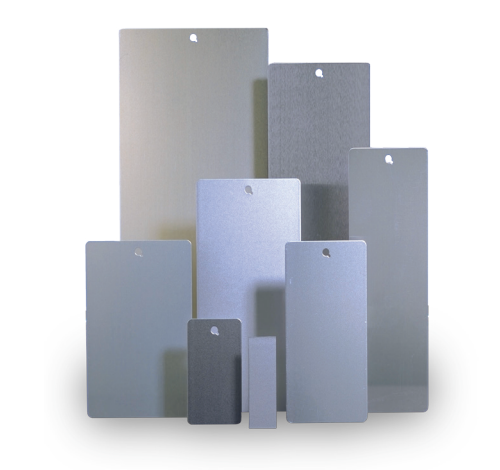
Sources of Variability
Surface problems can come from a number of sources:
- Surface texture varies with the condition of the rollers used by the steel mill to cold roll the steel to its final thickness.
- Surface cleanliness varies with the mill’s cleaning procedure, especially the procedures used to control carbon smut. All too often, carbon smut is actually baked onto the steel during the high temperature annealing process which follows rolling. This carbon smut is impossible to remove except by mechanical abrasion.
- Rust varies with the care taken in handling (a) at the steel mill, (b) during transport and storage, and (c) during fabrication.
- Steel stored for a long time with rust inhibiting oil will react to form an incomplete oxide known as oil stain.
The result is that ordinary steel is unsuitable for coatings tests. Although some commercial steel provides an excellent surface for coatings, you are just as likely to find steel which gives poor adhesion and poor rust resistance even with good coatings. In fact a single mill will often produce both very good and very poor surface quality, depending upon a number of uncontrolled factors. Cleaning and phosphating help, but they cannot overcome surface defects formed at the mill. In the early 1990s, researchers at The Sherwin-Williams Company published research in which coated metal panels were tested according to an alternating schedule of exposure in a fluorescent UV weathering test chamber (QUV ® tester) and to the Prohesion ® test. Their work led to the development of ASTM D5894 and ISO 11997-2. Follow-up studies confirmed that this method achieved better correlation to outdoor corrosion for several coating systems used in industrial maintenance applications. The method has been used and modified for highway construction and maintenance and in the petrochemical industry.
Controlling Variability
The Q-PANEL production process is specifically tailored to minimize the variability of steel surfaces.
- We buy all of our steel directly from a rare mill which is both willing and able to control surface quality. Moreover, our volume purchasing enables us to specify close tolerances on surface cleanliness and surface texture.
- Panels are cleaned, straightened, punched, and deburred in a continuous automated process.
- Rust and oil stain are controlled by rigorous inspection and by protecting the finished panels with vapor phase rust inhibitor and plastic bags.
Good Steel and Bad Steel, the Effect on Corrosion — a Classic Study
In a production environment it is very difficult to isolate the effect of steel quality on paint performance. However, an American car maker demonstrated the effect by cutting up a car body fresh off their production line, and then testing various parts of it in a salt fog chamber according to ASTM B117.
As is normal in a car plant, the steel in different parts of the body was from different production lots. However, the whole body had received the same pretreatment and painting: as a completely assembled unit it was cleaned, dip phosphated, electro-coated, primed and topcoated - all on the car maker’s normal finishing line. The photos below illustrate the substantial differences in corrosion performance that resulted from steel variation.
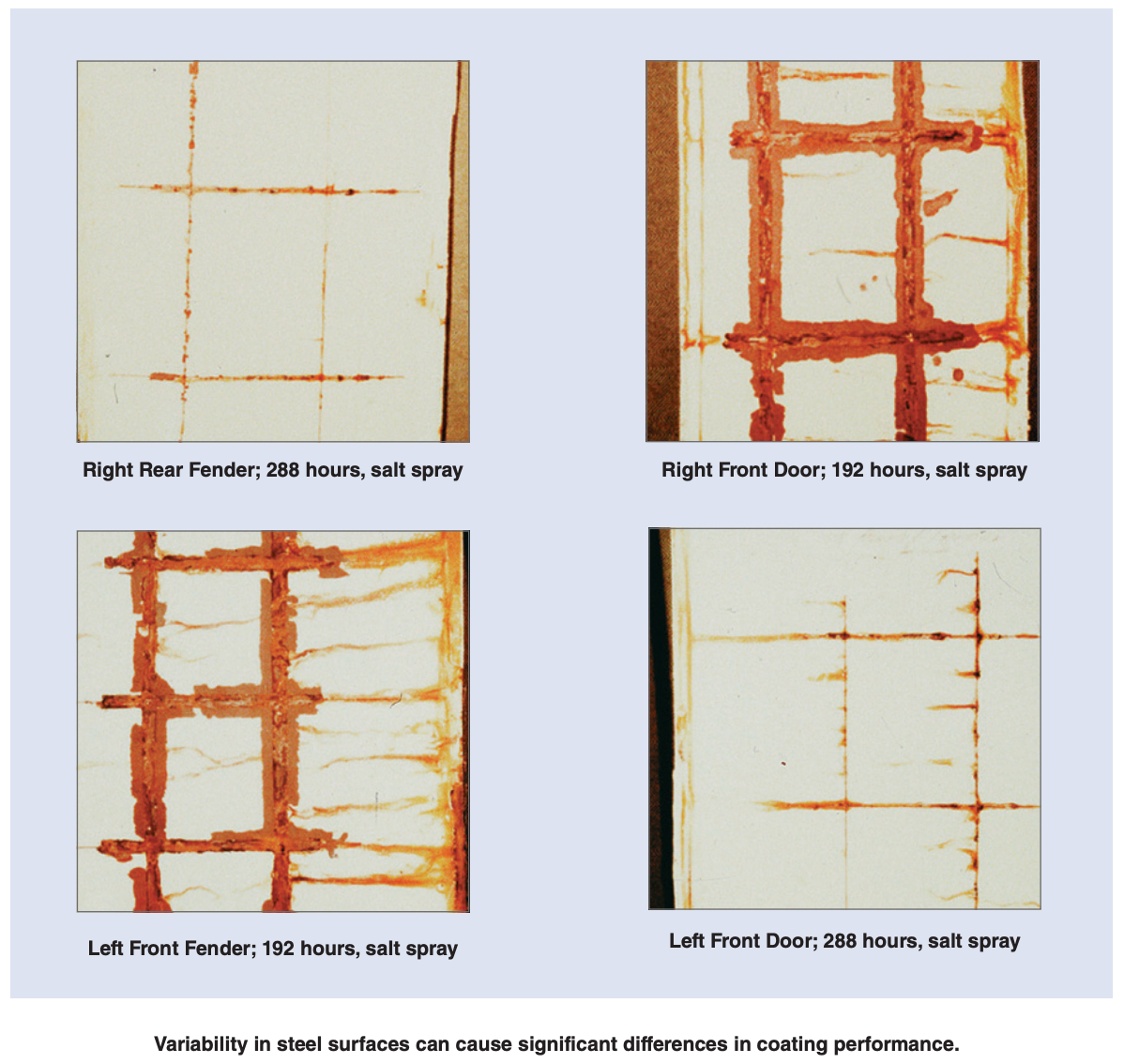