LP-0867 - Q-PANEL Applications Guide
Technical Bulletins
Posted 2023
Last Updated 2023
LP-0867
Q-PANEL Standard Substrate Applications Guide
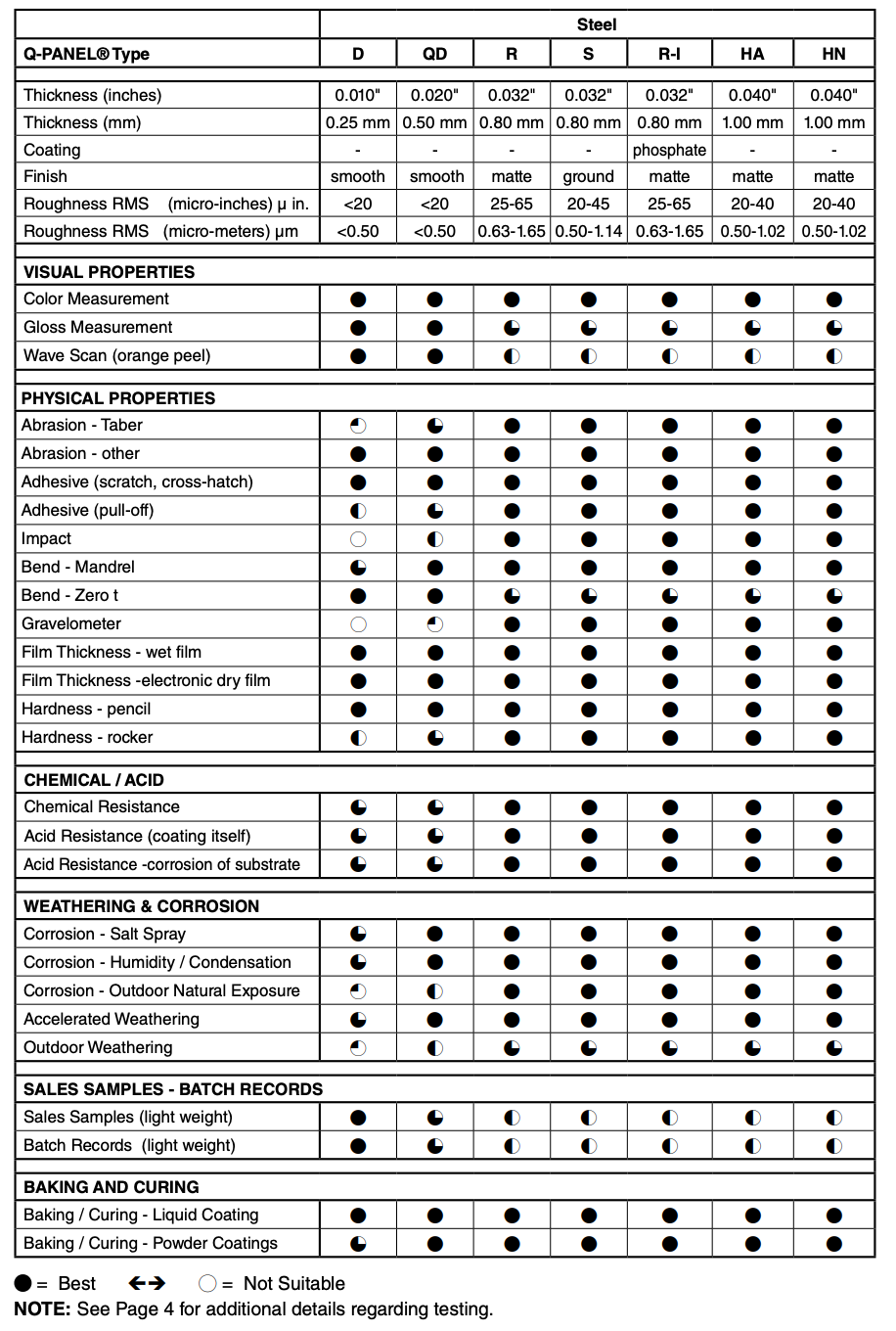
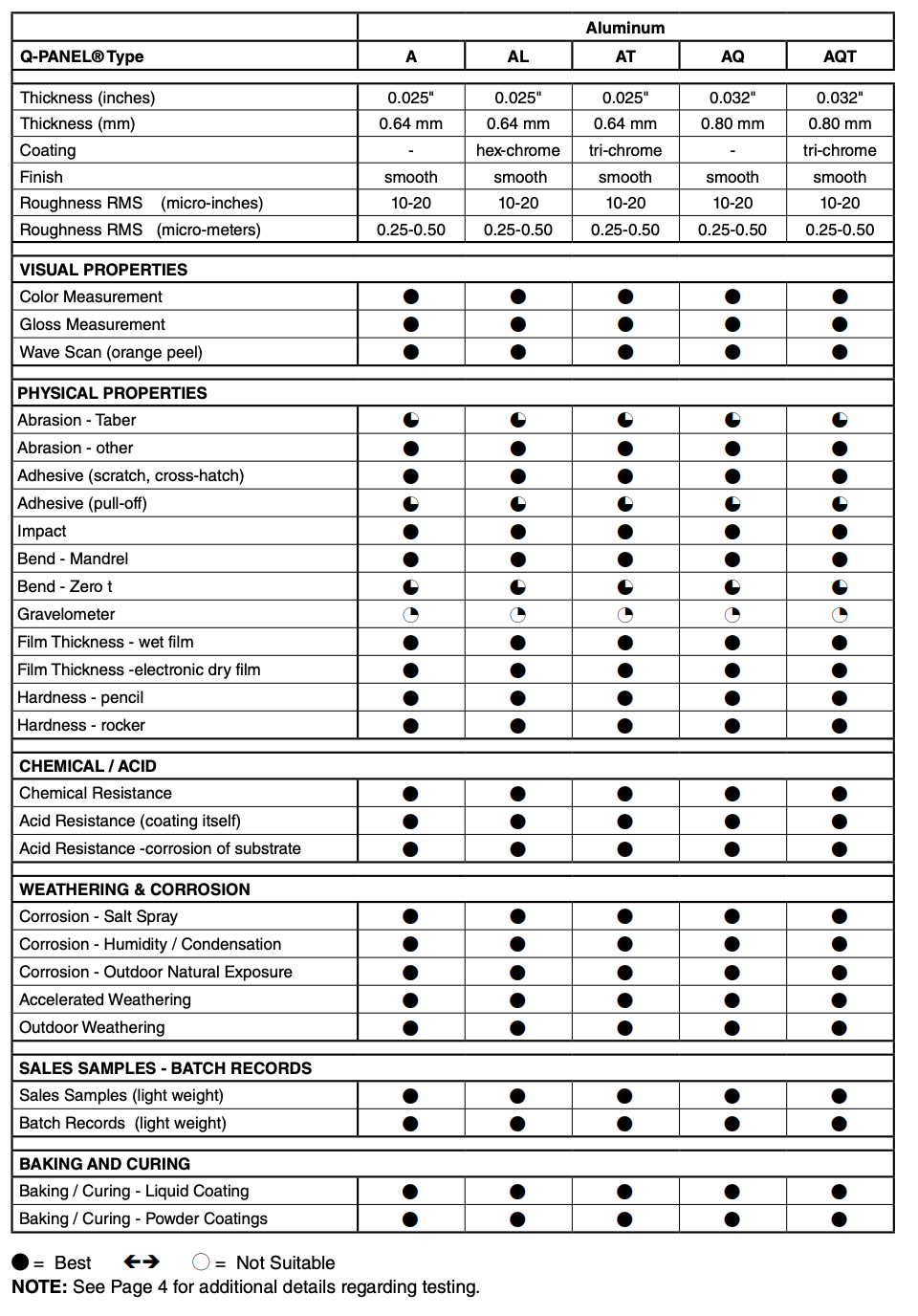
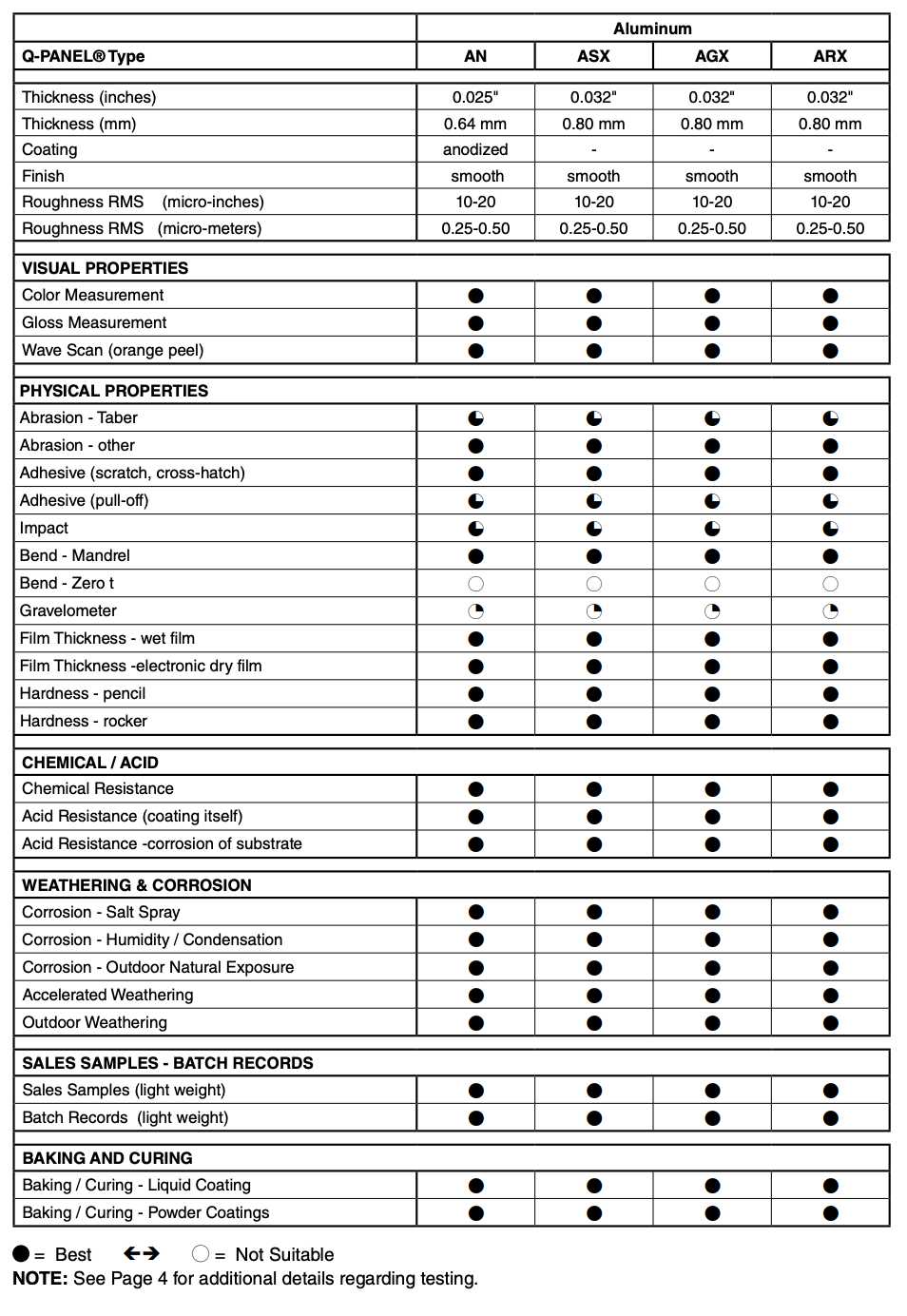
Q-PANEL Application Guide - Notes
Color Measurement, Haze Measurement: All types work well for most color and haze measurements.
Gloss Measurement: The texture of matte and ground surface panels may “telegraph” through some thin coatings.
Wave Scan (Orange Peel): This “Distinctness of Image” test requires an extremely smooth substrate. Recommend Type QD, D, A or AL. Surface texture of Type R, S, R-I, HA, and HN may “telegraph” through the coating.
Abrasion – Taber: Requires fairly strong and robust panel. Recommend Type R, S, or R-I.
Abrasion – Other: All types work well for most abrasion tests.
Adhesive – Scratch or Cross Hatch: All types work well for scratch adhesion.
Adhesive – Pull Off: Requires robust panel to prevent deformation during pull-off. Recommend R, S or R-I.
Impact: D is too thin; metal will often break in impact. QD, A, AT, AL, AN, AQ, and AQT will break in severe impacts. Use R, S or R-I.
Bend – Mandrel: Most panels will work for most mandrel bends. If bending with just your fingers, recommend D, A, AL, AT, AQ, or AQT, because they are thinner and easier to bend. If using a bending jig with a handle, you can use thicker steel panels.
Bend – Zero Thickness: Thinner panels like D and QD are easier to bend. A, AL, AQ, AT, and AQT can be used, but per EN 485-2, 3003-H14, and 5005-H24 are not recommended for 180o bend radius below 1.5T. Contact Q-Lab for details.
Gravelometer: D is too thin and will dent and deform badly upon gravel impact. QD, A, AT, AL, AN, AQ, and AQT will also usually deform too much. Deformation of the panel dissipates energy that is supposed to go into chipping the coating. Recommend R, S or R-I.
Film Thickness – Wet Film: Any type will work fine.
Film Thickness – Electronic Dry Film: Some electronic thickness instruments work only on steel or only on aluminum. Make sure the panel is made out of the appropriate metal for your instrument.
Hardness – Pencil: Any type will work fine.
Hardness - Rocker, Shore, Barcol, Pendulum: Any type will work fine.
Chemical Resistance: Any type will work fine.
Acid Resistance of Coating Itself: Any type will work fine.
Acid Resistance – Corrosion of Substrate: Use steel panels if end use is on steel; aluminum panels if end use is on aluminum.
Corrosion – Salt Spray and Humidity / Condensation: Use steel panels if end use is on steel, aluminum panels if end use is on aluminum. Sometimes Type D panels are too thin. When using steel panels, be sure to protect the back side to avoid extraneous corrosion that may contaminate the test.
Corrosion – Outdoor Natural Exposure: Use steel panels if end use is on steel, aluminum panels if end use is on aluminum. Thinner steel panels like D or QD may be subject to wind damage.
Accelerated Weathering: Most types work fine. Accelerated weathering usually does not produce corrosion, so the type of metal is not critical. Type A, AL, AT, AQ, and AQT are a little more convenient because the back does not need to be protected to prevent rust.
Outdoor Weathering: Thin panels like Type D or QD may be subject to wind damage. Type A, AL, AT, AQ, and AQT may also be subject to wind damage, but they have the advantage of being free from corrosion that can interfere with viewing gloss and color loss. Type R and S and R-I are thick and strong, so they resist wind damage.
However, remember to coat the back of steel panels to prevent extraneous corrosion. Type R-I panels produce better adhesion because of the phosphate coating.
Samples and Batch Records: Most people prefer the lightest panels; Type D, A, AL, or AT. Type AL or AT panels usually provide better adhesion because they have a chromate pretreatment, so the paint will be less likely to scratch off.
Baking and Curing: Most types work fine. However, some types of powder coatings require a substrate with more mass than is found in the very thin Type D.