LL-9030 Evaluation of Weathering Effects: Visual Inspections and Instrumental Measurements
Technical Bulletins
Posted 2023
Last Updated 2023
LL-9030
It is important to properly quantify the results of any exposure testing program. Typically, the client is interested in the type and/or amount of change in a material's properties. Change in some prop - erties, for example color or gloss, can be measured using the proper instruments. Other changes such as cracking, peeling, chalking, blistering and rusting, can be evaluated visually and rated according to standard rating scales from ASTM or other technical organizations.
Frequency of Inspections
Typically, the property of interest is measured, or rated, prior to exposure. Thereafter, periodic inspection and evaluation are necessary to quantify the progress of the test. For outdoor exposure tests, inspections are com - monly performed on a monthly or quarterly basis. For accelerated laboratory tests, evaluations are often performed every 100 or 250 hours. The inspection results are used to monitor the degradation over time. This is a crucial part of a comprehensive testing program.
Visual Inspections 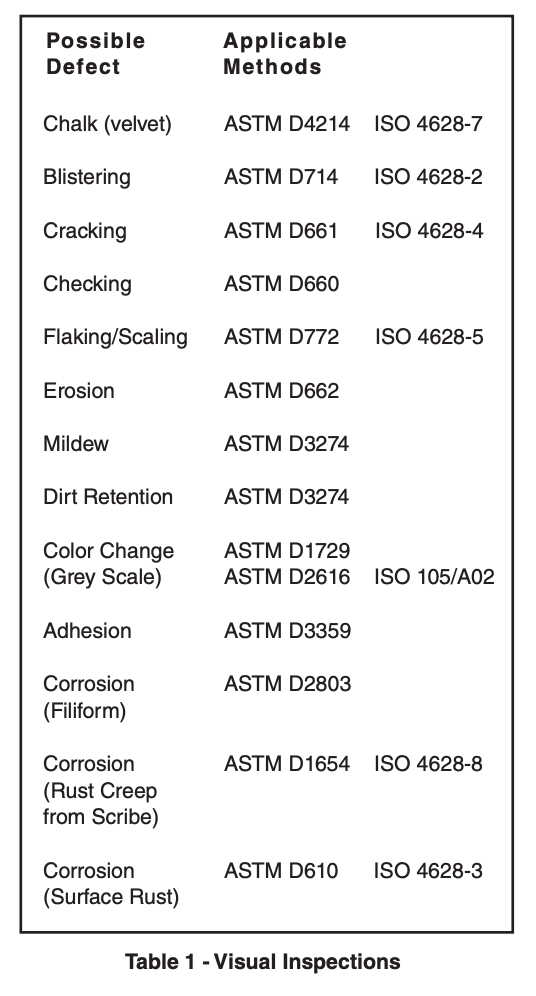
Although visual inspections are subjective, they are extremely vital, for it is often the perception of the individual end user that will determine whether a material’s appearance is satisfactory. Visual inspec - tions must be repeatable and consistent with several other people’s perceptions. Because consistency is critical, visual inspections must be performed by a trained and experienced inspector.
When a customer requests a visual inspection of a test specimen, the inspector will check for all observable defects, including those listed in Table 1. The inspector will rate the change according to the applicable scale. Visual inspections of weathering effects are typically reported using the standard ASTM 10 to zero rating system, as shown in Table 2 (following page).
The pictorial standards depicted in the Federation of Societies for Coatings Technology (FSCT) book, Pictorial Standards of Coatings Defects, are used to directly compare the defects on the test specimen with a defined numerical value. 1 This assists the inspectors in producing repeatable evaluations and aids the client in visualizing the reported defect.
Visual ratings are performed under standard lighting conditions, using the naked eye. Microscopic evaluations (up to 10x) are used for confirmation or when - ever necessary, as in the case of micro-checking.
Instrumental Measurements of Appearance Properties
Appearance is a critical attribute for many products and materials. The customer’s perception of quality is often based on gloss, color, brightness, smooth - ness or some other appearance characteristic. Useful service life is often determined by these same characteristics. A product that is otherwise perfectly serviceable will often be discarded when its appearance fails to meet the customer’s aesthetic requirements.
Since, by definition, appearance is a visual or aesthetic characteristic, it seems to be a contradiction to use instruments to measure it. However, appearance is usually a property of the surface (smoothness, reflectivity, color, etc.). Over the years, instruments have been refined to closely agree with the human observation.
Instrument measurements of appearance are objective and have several advantages over the subjective visual evaluations. Instrumental measurements provide a quantifiable measure of performance. They preclude the possibility of human bias because a machine will produce the same numeric values every time, if all con - ditions are repeated. Additionally, the numbers produced by these instruments form a continuous scale to which a number of statistical operations can be applied. In the weathering industry gloss, Distinctness of Image (DOI) and color are measured using electro-optical instruments. These are used to monitor the surface appearance properties of unexposed and exposed materials to gauge the useful life of a product.
Specimen Cleaning
For outdoor weathering tests, it is strongly recommended that all instrumental measurements on weathered surfaces be performed on a washed specimen section. All of these measurements are highly sensitive to surface attachments, such as dirt and mildew. These particles form a barrier layer over the test surface, and prevent the instrument from measuring the true surface. If the surface is dirty, the instrument will measure the dirt, not the surface.
Gloss Measurements
Measurements of gloss are an essential part of many evaluation programs. They are particularly important for paints and plastics. Gloss is one of the first properties that is affected during weathering exposure. It is also one of the first aspects of appearance that appeals to the observer.
Instrumental gloss is the most widely used form of electro-optical surface appearance measurement. Instrumental gloss measures the overall shine of a surface. A gloss measurement consists of shin - ing a beam of light onto a surface at a fixed angle and then sensing the percentage of that light that reflects at exactly the opposite angle (instead of scattering). A perfectly smooth surface would reflect everything at the angle of incidence and would therefore have a gloss value of 100.
Any surface roughness or other imperfection will cause a percentage of the light beam to scatter. This will reduce the amount of light that is recap - tured, and therefore reduce the gloss value. The gloss angle refers to the angle (relative to the vertical) at which the light beam strikes the surface. The most common gloss angles are indicated in the illustration below.
For a complete discussion of gloss measurement, consult ASTM D523 or ISO 2813.
Distinctness of Image (DOI) Measurements
When we look at an automotive paint finish, we see reflected images. The more clearly defined those images are, the better we feel about the fin - ish. Distinctness of image is easily affected by surface deterioration, such as ripples, orange peel, micro-scratches, hazing, etc.
DOI is a specialized, more precise form of gloss measurement, using a 30 degree reflection angle. DOI uses a narrow, very highly focused light beam. Regular gloss utilizes a much wider light beam. The DOI sensor measures the sharpness of the edge of the light beam and uses a 100-point scale, where perfect distinctness of image is 100. For a complete discussion of DOI measurement, consult ASTM E430
Color Measurements
Instrumental color is the most complicated of all the electro-optical measurements. Color measurements are made by shining a light on the specimen and collecting the light which is reflected from the specimen. The continuous spectrum of the reflected light is used in a mathematical transformation to create three values which are used as a shorthand to describe the color of the measured object.
L, a, b, Color Space
Most instrumental color readings use some form of the L,a,b, color space to define color. With L,a,b, three numbers are used to describe a color. Each of the three numbers refers to one of the corresponding coordinates:
Lightness Factor (L). The measured object’s lightness or darkness is quantified by the “L” number on a scale of zero to 100, where 0=black, 50=grey and 100=white.
Red/Green Factor (a). The object’s redness or greenness is quantified by the “a” number. When the “a” value is a positive number, the measured object is a red color. The higher the number, the more red the object is. When an “a” is a negative number, the measured object is a green color. The larger the negative number, the greener the color. A value of zero for “a” would be exactly intermediate between red and green.
Blue/Yellow Factor (b). The object’s yellowness or blueness is quantified by the “b” number. When the “b” is a positive number, the object is yellow. The larger the number, the more yellow the object. When the “b” value is a negative number, a blue colored object is indicated. The larger the number, the more intense the color. A value of zero would be intermediate between yellow and blue.
Any color can be described by its L,a,b, coordinates. For example, a mauve color could have a “L” value greater than 50, a positive “a” value (red) and a negative “b” value (blue).
Color Measurement Issues
Unlike gloss and DOI, there are a number of fundamental variations in the measurement conditions that can be used when making color measurements. In addition, there are several different types of color measurement instruments in common use. Each will give slightly different measurements.
For comparable measurements, each of the following measurement parameters must be consistent, and therefore should be specified when starting your weathering program:
Geometry (Directional or Diffuse). Color measurements are made by shining a light on the specimen and analyzing the spectrum of reflected light to generate the L,a,b, numbers. Depending on the instrument type, the light sensor is either a directional unit or a sphere. Directional units (often referred to as reflectance units) are usually described by the angle of incidence/reflection at the point of measurement; for example, 45/0 or 0/45.
Observer Angle. This is a straight choice between older and newer technology. Older color instruments used only a 2-degree observer. Newer devices use the 10-degree observer. Many newer instruments allow a choice to enable comparison with older devices.
Illuminant. Any one of several different light sources may be simulated to illuminate the specimen during measurement. Different illuminants may give different results. Illuminant D65, the most commonly used, represents noon daylight.
Specular Component. The specular component is the glossy reflection that the illuminant produces. On sphere instruments the specular component may be either included or excluded from the reflected light. The specular component is always excluded when using directional devices (e.g., 0/45 geometry.
Calculations of Color Change. Color change is calculated as the difference in the L,a,b, values before and after exposure. The term “delta” (∆) is used to denote the difference, that is, current measurement minus original measurement. The larger the ∆ number, the larger the color change. Thus, ∆L is the change in the Lightness factor. ∆a and ∆b are treated in the same manner:
- +∆L means there has been a lightening of color
- -∆L means there has been a darkening of color
- +∆a means more red (less green)
- -∆a means more green (less red)
- +∆b means more yellow (less blue)
- -∆b means more blue (less yellow)
A total color change value of delta E (∆E) is calculated as a composite of all three factors, and is widely used as pass-fail criteria for exposed materials.
Color Scales. The color of the measured object is normally reported in one of several recognized color scales: CIE L*a*b*; Hunter L,a,b,; or CIE XYZ. The CIE and Hunter L,a,b, scales are widely used and based on similar calculations. The XYZ numbers are known as tristimulus values. Certain specialized color indexes are also used to determine specific changes. Yellowness Index (YI) and Whiteness Index (WI) are used to evaluate color on near-white opaque materials, such as TiO2 pigments. These scale were originally visual, but have been converted into instrumental, calculated values to compare with the old visual data.
For a discussion of instrumental color measurement, consult ASTM D2244. Excellent publications on the theory and practice of color measurement are available from all of the major color measurement equipment manufacturers.
Conclusion
Because useful service life is often based on aesthetic or other visual considerations, it is frequently important to quantify any changes in the appearance of a weathered test specimen. There are a number of techniques available. Visual inspections, if performed by an expert, allow good qualitative and quantitative ratings. When applicable, instrumental measurements are especially useful because of their objectivity. Both visual and instrumental evaluations are crucial to a comprehensive testing program.