LX-5018 - Accelerated Testing for 21st Century
Last Updated 2014
Automotive OEMs, coatings material suppliers, and weathering specialists banded together in a series of studies aimed at improving weathering test protocols. After a decade of research, the result is a newly published ASTM test standard, D7869, which has been shown to provide very good correlation to outdoor Florida test results for several failure mechanisms seen in a variety of automotive and aerospace coatings technologies. This new method validates the idea that accelerated testing can accurately replicate the effects of outdoor weathering, but the long path to this result demonstrates that correlating to the natural environment is never a simple proposition.
The studies discussed in this paper focus on four areas:
- Xenon arc methods in the automotive industry were written specifically to be run in two models from one manufacturer. Recognizing that this approach stifled innovation and that the discontinuation of these models in the market raised questions about test reproducibility in newer models, Chrysler led efforts at the Society of Automotive Engineers (SAE) to implement performancebased test standards which allow the use of any chamber design that meets the specified test conditions.
- Ford examined the role of spectral mismatches between natural sunlight and commonly used xenon arc optical filters and their effect on accurately reproducing photo-oxidation in an accelerated weathering test. A new filter was implemented in the xenon arc chamber industry and is required by ASTM D7869.
- A coalition of automotive coatings material suppliers, BASF and Bayer, and Q-Lab looked at the importance of moisture in both the outdoor Florida environment and in xenon arc test chambers. It became clear that the existing standard did a poor job of simulating moisture absorption outdoors.
- Ford again stepped in to expand the work on moisture and create a new test cycle for xenon arc testers that accurately reproduced all of the degradation mechanisms caused by weathering, using the new optical filter developed earlier. The new cycle incorporates a novel combination of moisture exposure from common fluorescent UV standards and rapid cycling common in previous xenon arc standards.
In reviewing this previous work, this paper will explore the state of weathering science at the turn of the 21st Century and the technical and organizational challenges overcome in the long path to the new breakthrough test method.
Introduction: The Early Days of Automotive Accelerated Weathering
In the 1970’s, most automotive coatings underwent laboratory weathering testing with carbon arc or fluorescent UVB lamp technology. Although these light sources do not provide an accurate match to the ultraviolet portion of sunlight, the tests provided good correlation to outdoor weathering for the coatings technologies dominant in the automotive industry at that time. However, changes to coatings technologies in the 1980s required a better spectral match to sunlight.
As a result, carbon arc tests were replaced by xenon arc tests, and the UVA-340 lamp was developed for fluorescent UV test chambers. In 1989, the Society of Automotive Engineers (SAE) published the first international standards for xenon arc weathering in the automotive industry, J1885 and J1960 for interior and exterior materials, respectively. These test standards were written for two specific water cooled xenon arc test chamber models designed with a vertical lamp and rotating specimen rack. While xenon test standards came to dominate automotive approval protocols, fluorescent UV testers proliferated in laboratories performing research and development or general quality control, where both UVA and the older UVB technologies were employed and still are to this day.
The early xenon arc tests, although a significant improvement over the older carbon arc tests, were of limited use in predicting long term durability. Although test results using these early SAE standards generally correlated well with outdoor Florida results for color and gloss loss, they did not correlate well for many important degradation modes, such as the costly problem of delamination. Because of this, attempts to predict real world performance with these laboratory methods often failed. Simply stated, results from these hardwarebased test standards did not correlate well with outdoor test results or the experiences of some unhappy customers.
Breaking the Innovation Logjam: The Chrysler Studies
Xenon arc weathering technology showed great promise because of its potential to reproduce sunlight accurately, but one consequence of the first SAE standards was that technological innovation was stifled, making it very difficult to improve correlation between laboratory and outdoor weathering. The hardware specific standards created a market barrier to improvements in technology. The lack of variety among test chamber designs meant that the status quo remained largely unchallenged. Poor correlation between outdoor and laboratory weathering tests thus became institutionalized by the standards.
Recognizing that this approach stymied innovation, a few OEMs and coatings suppliers, led by Chrysler, created a new “performance-based” approach that broke the innovation logjam with the publication of SAE standards J2412 and J25271. A performance-based standard is one that relies on a thorough technical description of the environmental conditions of the test rather than specifying a particular device and listing the required settings. Writing these technical descriptions of the environmental conditions, the backbone of any performance-based standard, is more difficult than the hardware-specific approach.
The controversy over these SAE standards centered on the use of flat array, air cooled xenon arc test chambers. The old standards required the use of rotating rack chambers that feature water cooling of the xenon lamp, and some in the industry expressed concern that the flat array chambers would produce different results than the rotating rack designs. Others in the industry wondered if newer design rotating rack testers delivered equivalent results compared to their predecessors.
In order to provide an objective and scientifically valid method to establish that different models available in the market generated similar results with these specific standards, SAE standard J2413 was developed. This standard required that test chambers must demonstrate compliance to the specified test conditions, repeatability, reproducibility, and degradation of standard reference materials within a certain range and with an acceptable level of uniformity within the chamber. Repeatability refers to achieving similar results in multiple tests within a single chamber, while reproducibility refers to achieving similar results in multiple chambers.
To address questions about within-chamber uniformity, Q-Lab enlisted the participation of ISO 17025 accredited laboratories operated by BASF and ACT Laboratories to conduct the largest study ever published on the subject. The goal was to compare the uniformity of degradation of a wide variety of standard reference and other common automotive materials. Three different rotating rack xenon arc models and one flat array model were part of the study. For illustrative purposes, schematics of the two configurations are reproduced from the original study in Figure 1.
The main advantage of a rotating rack design is that specimens are automatically rotated around the light source, effectively eliminating variability of conditions from side to side. The design does not eliminate variability that could exist from top to bottom, however. As discussed below, repositioning of specimens in the vertical direction of a rotating rack chamber is recommended by the latest xenon arc standard. In flat array testers, also known as static array testers, specimens should be manually repositioned to reduce the effects of non-uniformity across the exposure area. In the published study, tests in the flat array devices were performed with and without specimen repositioning.
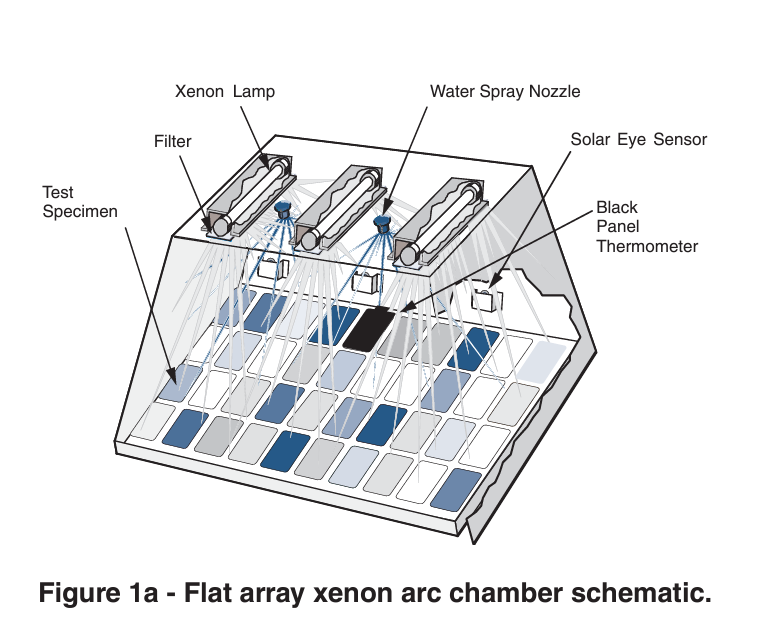
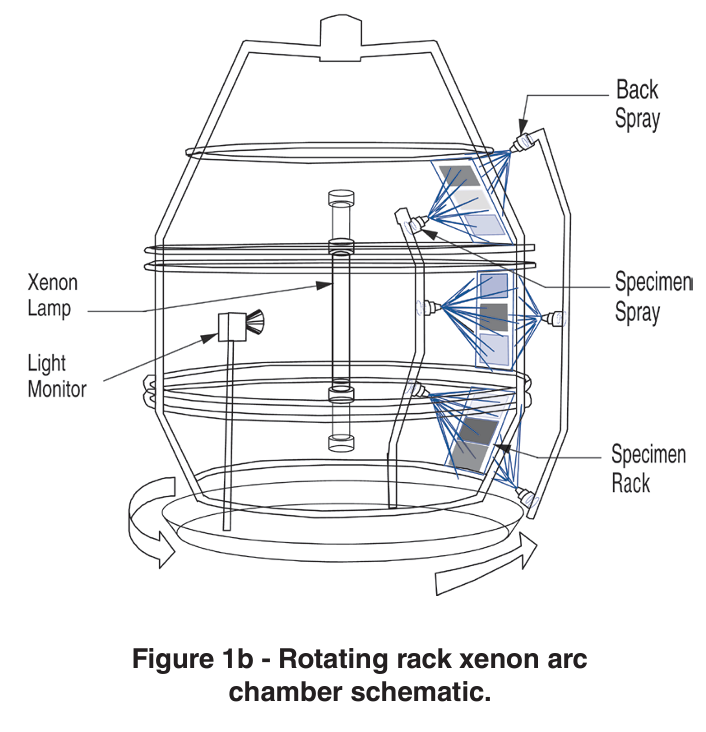
The results of the study, reproduced in Table 1, show that uniformity of the flat array and rotating rack testers was similar. As expected, manual repositioning of specimens in the flat array testers improved uniformity. Interestingly, even without repositioning, the flat array uniformity was better than rotating rack uniformity in some cases. The study notes that the results include variability of measurements and materials.
In anticipation of the publication of SAE J2412 and J2527, Chrysler sought to use the J2413 protocol to compare results of a flat array tester, the Q-SUN® Xe-3-HS from Q-Lab, and the Atlas Ci65A, one of the two rotating rack test chambers specified in the old SAE standards. It selected 37 automotive exterior grade materials and reference materials for this study and chose BASF’s Southfield, Michigan laboratory to run the tests.
The first round of testing found some differences in degradation between the flat array and rotating rack testers, particularly in some of the plastic specimens. An investigation into the causes revealed some subtle design differences not captured in the performance-based standards. First, the flat array tester utilized an anodized aluminum black panel thermometer, while the rotating rack tester had one made with painted stainless steel. Although ultimate temperature readings were very similar, there was a significant difference in response rates of each sensor. Plastic materials reached higher temperatures during transition periods of the test cycle when an aluminum black panel was used in comparison to a painted steel panel. In addition, placement of the chamber air temperature sensor relative to the air flow was not defined in the standards, but this proved to be a very important factor that affected specimen temperature and degradation results.
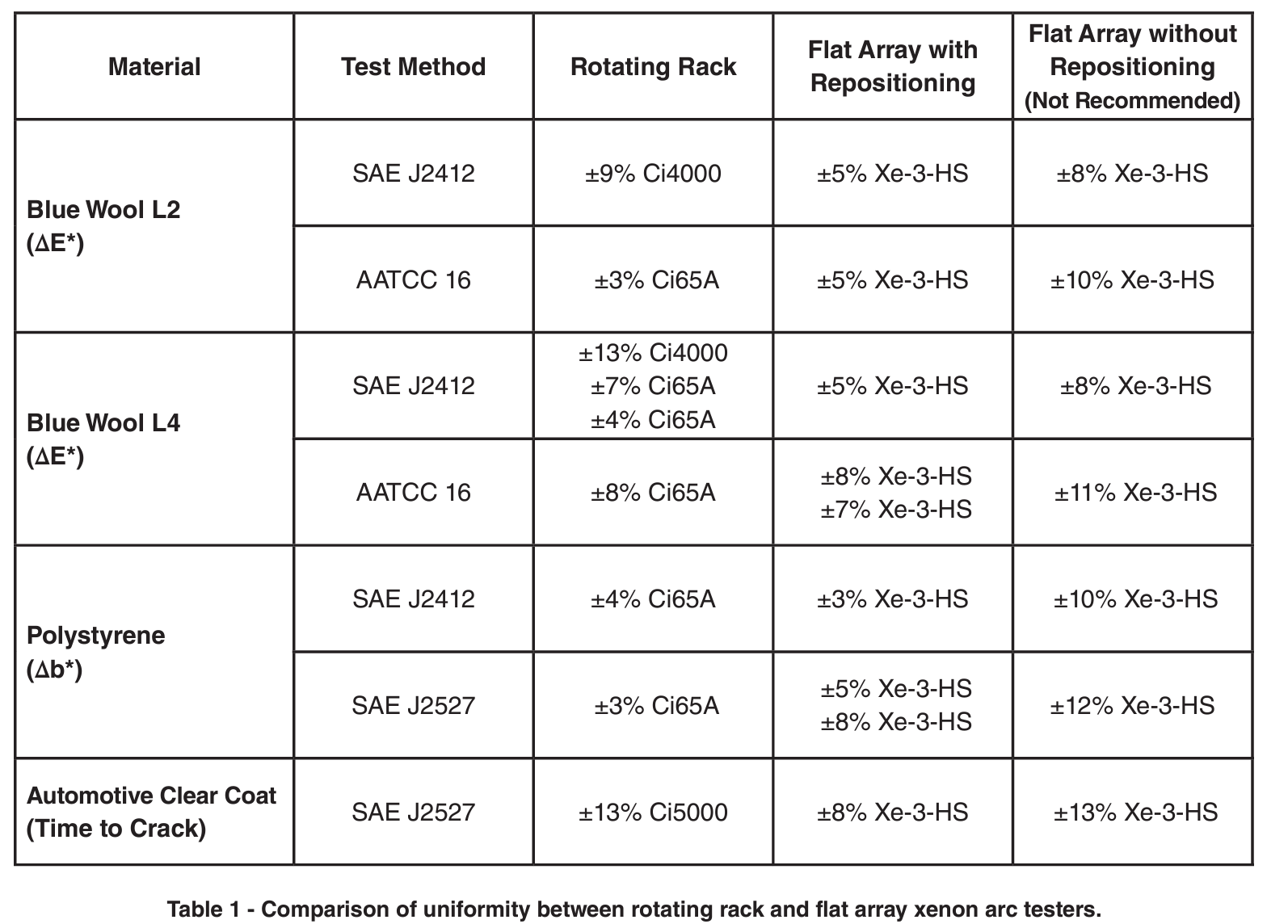
Finally, the flat array tester delivered significantly more water than the rotating rack. This is because the rotating rack featured a single set of nozzles that spray specimens for a few seconds during each revolution of the rack. The flat array was programmed to spray 20 seconds of each minute, which resulted in much more water delivered to specimens. This fact proved critical in the research that created the most recent xenon arc weathering standard.
After some design modifications to the flat array, including reducing the spray time to 5 seconds of each minute, a second round of tests was performed. Specimens were selected from the first round which included all of those that exhibited differences in the two testers, some specimens which had achieved very similar results in both testers, and new specimens that were known to be sensitive to heat or moisture. This round showed excellent correlation between the two testers. This proved that flat array testers could produce very similar results to rotating rack testers and that the implementation of performancebased standards need not compromise reproducibility of test results.
The Importance of Optical Filters: The Early Ford Studies
These first performance-based automotive standards were firmly planted in both the old and new eras. Test cycles remained unchanged, and results were expected to be similar to tests run under the old standards. The authors of the Chrysler paper noted that the goal of the project was to have the flat array tester achieve the same degradation as a rotating rack tester, but not necessarily match outdoor weathering. This is a continuing legacy from the era of hardware-based standards.
The importance of the new performance-based standards was that users of weathering chambers could freely choose the design that best suited their particular needs, and that the industry was open to new approaches. However, these standards did not address the challenge of correlation to outdoor weathering. Suppliers of xenon arc weathering chambers were forced to compromise their designs so that test results were comparable to the old methods. These compromises included using optical filters which did not produce the best possible match to the sunlight spectrum.
Around the same time that Chrysler and other SAE participants were creating the new performance-based standards, Ford was looking at improving correlation between xenon arc weathering exposures and outdoor weathering. It conducted studies that examined the effect of the spectral cut-on wavelength of various xenon arc optical filter systems on photo-oxidation rates in comparison to south Florida exposures. The studies showed that even small spectral mismatches at the cut-on wavelength could produce significant discrepancies in photo-oxidation, resulting in erroneous test results.
The researchers at Ford and other companies used a fingerprint technique that examined data from Photoacoustic Fourier Transform Infrared (PAS-FTIR) spectra. They began by identifying four peaks in the –OH and –NH region of the IR spectrum that shifted due to the effects of weathering. These peaks were called a, b, c, and d, respectively. The ratio of the heights of peak a to peak b was calculated, as was the c to d ratio. These ratios were plotted against each other. The result is a line with a given slope that represented the balance of degradation reactions from weathering. A comparison can be made of the slope created by any given accelerated test to the slope from an outdoor exposure, and this slope can be called the exposure’s photo-oxidation fingerprint. The closer these two fingerprints are, the more accurate is the accelerated test in reproducing photo-oxidation.
Commonly used xenon arc optical filter systems in the automotive industry are known by names such as Quartz/Boro, Extended UV - Q/B, Boro/Boro, or Daylight – B/B. The first two allow significantly shorter wavelengths than natural sunlight. The latter two also transmit shorter wavelengths than natural sunlight, but the mismatch is less severe. Some of this early work by Ford demonstrated how the presence of short wavelength UV energy, below the natural sunlight cut-on, caused unrealistic photo-oxidation which could create misleading test results. False positives or false negatives could result from the spectral mismatch issue inherent in the old hardware-based xenon standards and their subsequent performance-based rewrites.
Figure 2 shows the results of some of this early work. A Fresnel Sunlight Concentrator uses natural sunlight and mirrors to create a high irradiance exposure. Because it is using natural sunlight, there is negligible spectral mismatch to real outdoor conditions. This particular light source produced a good fingerprint match to the natural south Florida exposures. Other common light sources, including those used in the SAE xenon arc standards, are also shown.
Ford looked at other common “daylight” filters on the market, some of which have a better match to the natural sunlight cut-on than the Daylight B/B (boro/ boro). Because the photo-oxidation fingerprints from these filters did not provide a close enough match, Ford sought an improved optical filter.
The 3M Company brought into the mainstream an optical filter that was a good candidate. Although new to the weathering industry, this type had been in use in the biomedical field for testing the effects of pharmacological compounds on sunlight induced erythema. Ford conducted tests using this optical filter and found its photo-oxidation fingerprint was a better match to south Florida results6. See Figure 3 and Figure 4.
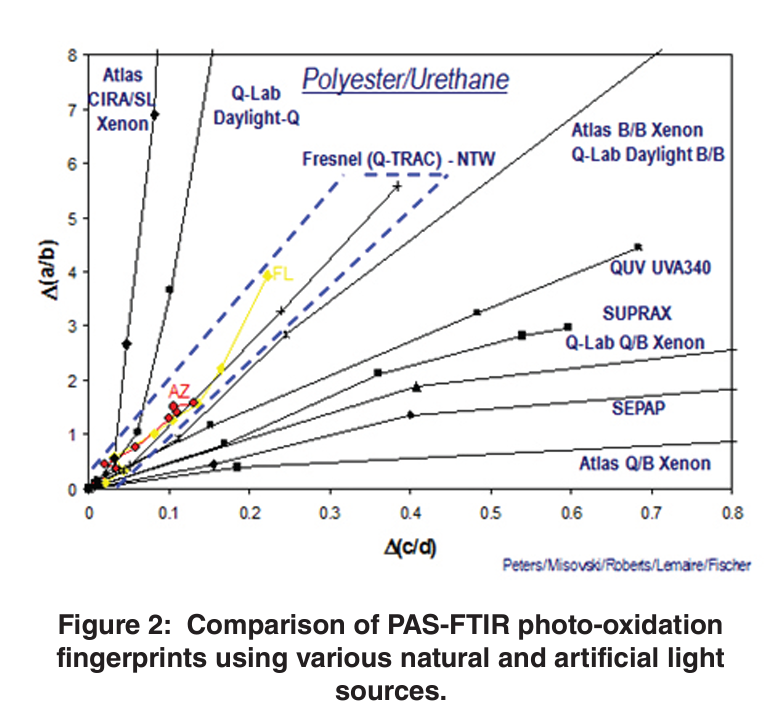
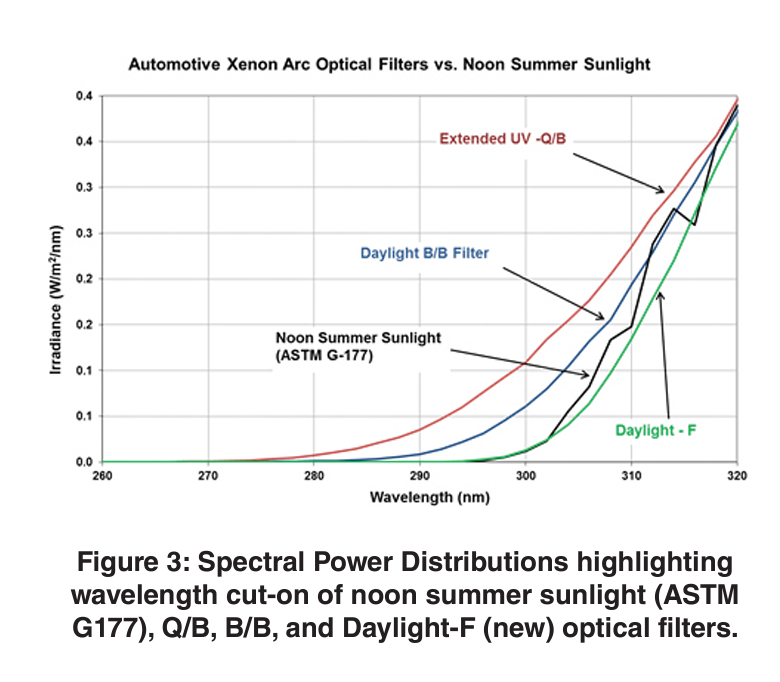
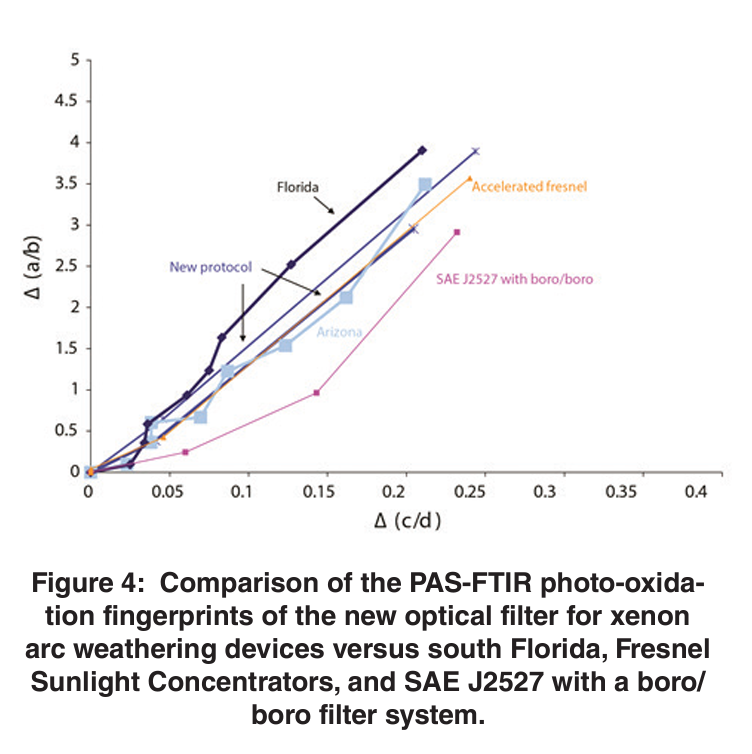
Photo-Oxidation is Only Half the Battle: The BASF, Bayer, Q-Lab Acid Etch and Moisture Studies
An early success of the new era of performance- based xenon arc test methods in the automotive industry was publication of ASTM D7356, Standard Test Method for Accelerated Acid Etch Weathering of Automotive Clearcoats Using a Xenon-Arc Exposure Device. Based on research performed by BASF and Q-Lab, this test utilized the new flat array testers to reproduce acid etch of automotive clear coats that occurred during a summer of exposure in the acid rain environment of Jacksonville, Florida4. A Q-SUN Xe-3-HS model was modified to include a secondary spraying system to deliver a dilute acid solution to the specimens. The flat array design was important for this research because it allowed slow dry-off of dilute acid solution into concentrated droplets which degraded the clear coat. BASF had observed that acid etch failures in the field were almost exclusively on horizontal surfaces such as hoods and trunks and rarely on vertical surfaces such as doors and fenders, so the flat array tester, slightly modified to have a horizontal specimen surface, was a logical choice for reproducing acid etch in the laboratory. The new method, which simulated a season of Jacksonville exposure in a few hundred hours, was a breakthrough to suppliers who needed a laboratory method to speed product development and reduce risk of field failures and unhappy customers
Although this study focused on one specific failure mechanism, the project was a stepping stone in the development of better accelerated weathering tests. From an organizational perspective, this project continued some of the working relationships that began during the Chrysler studies and that carried into later studies. The project also enticed additional research partners. From a technical standpoint, development of the test cycle required careful analysis of the moisture environment in which degradation occurs. See Table 2. The methodology of translating the outdoor moisture environment into conditions in a xenon arc test chamber was duplicated in subsequent research, and elements of the test cycle developed were incorporated into improved general weathering cycles. See Table 3. In particular, the cycle begins with an extended period of darkness after the initial application of acid solution.
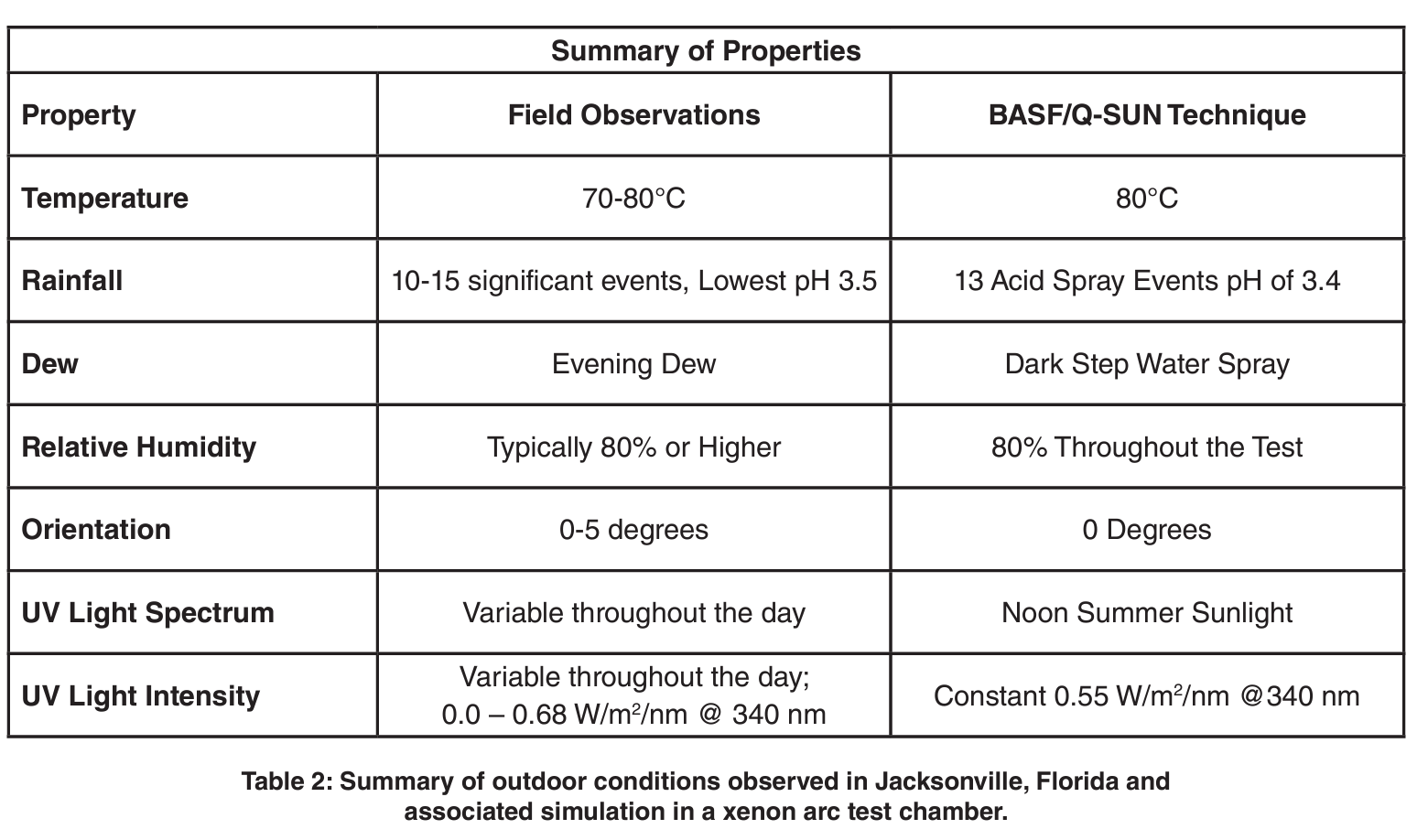
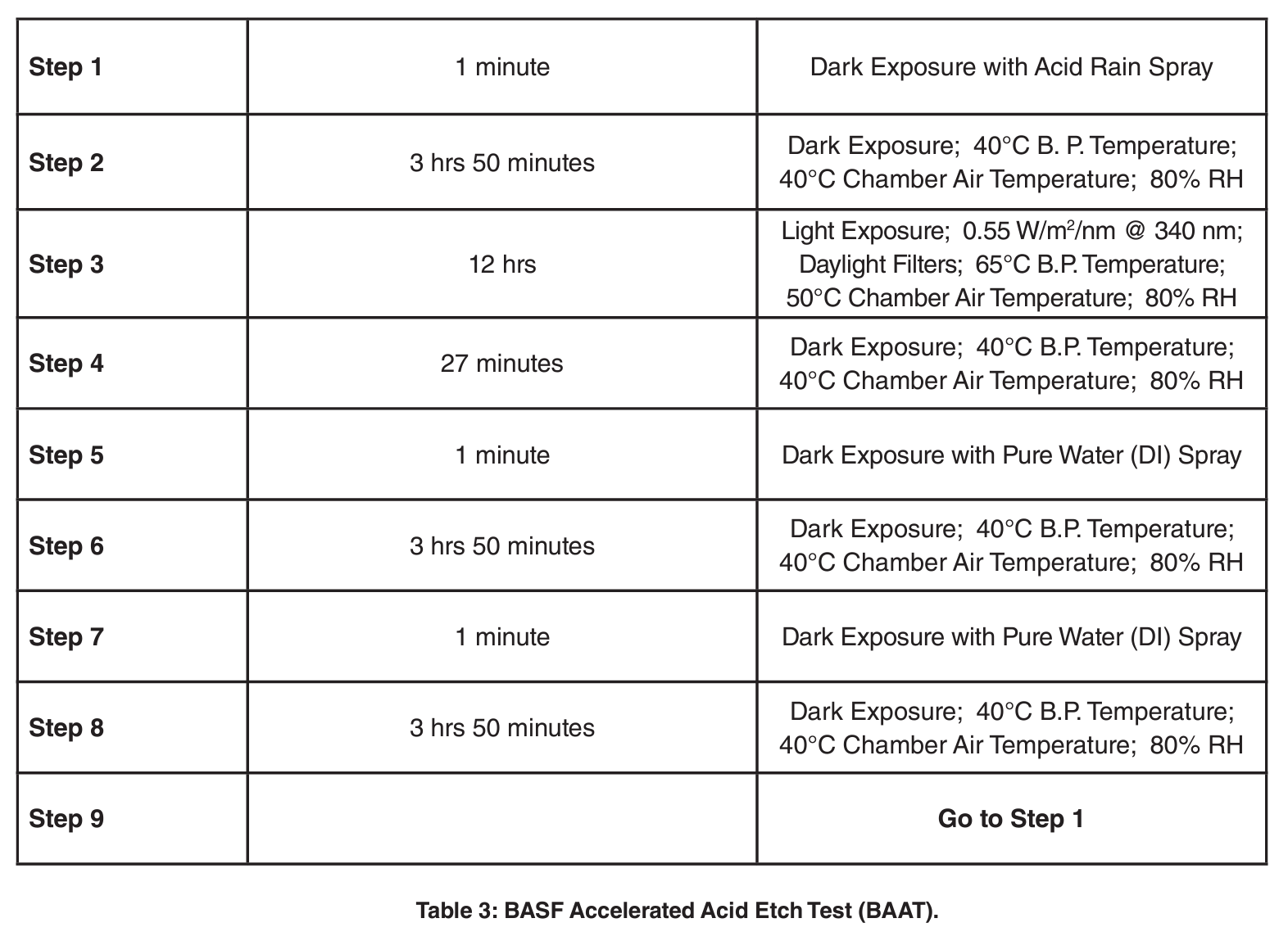
Near the end of the acid etch project, BASF partnered with Bayer to build on the research into outdoor moisture. Bayer maintained a weathering exposure site on Blount Island in Jacksonville, Florida. The two suppliers to the automotive coatings industry wanted to determine how much moisture a coating absorbed in the Florida environment, the conditions that caused moisture uptake, and if the SAE standards (old J1960 and new J2527) replicated these mechanisms. It was theorized that the SAE standards did not emulate outdoor moisture accurately, and that this was the reason why blisters, delamination, and cracking that were sometimes seen in outdoor Florida results and field reports were not replicated in the xenon arc tests.
Similar Time of Wetness (TOW) studies were performed by Q-Lab in the 1970s. These studies were built upon the development of the Cleveland Condensation Tester (QCT®) by Q-Lab and the Cleveland Coatings Society in the 1960s. These studies demonstrated that painted panels in the Florida environment maintained liquid water on the surface greater than 50% of the time7. Furthermore, the primary cause of wetness was dew formation, not rain. The original QUV® accelerated weathering tester was designed as an extension of the QCT. The condensation function of fluorescent UV weathering chambers was a primary reason the technology was so widely adopted by the coatings industry in the 1970’s and 1980’s. Much of the progress in xenon arc testing during the first decade of the 21st century has resulted from the pursuit of achieving moisture performance similar to fluorescent UV testers.
The BASF and Bayer studies, published as “The Flaws in Accelerated Weathering of Automotive OEM Coatings,” took the TOW studies further by developing techniques to measure the mass of water absorbed into a coating. In addition, the researchers were able to correlate water absorption and release with ambient temperature, relative humidity, and rainfall. This was accomplished by using a load cell that recorded the mass of a panel over time. They determined that the SAE cycle resulted in significantly less moisture uptake than the Florida environment. The researchers also pointed out other flaws concerning the cycle3, shown in Table 4, and water uptake data is highlighted. On average, the SAE cycle produced approximately one fifth the water uptake seen in a wet Florida day. The maximum moisture uptake possible in an automotive coating could be determined by an immersion test (extended soak) or by a standard condensation exposure (QCT).
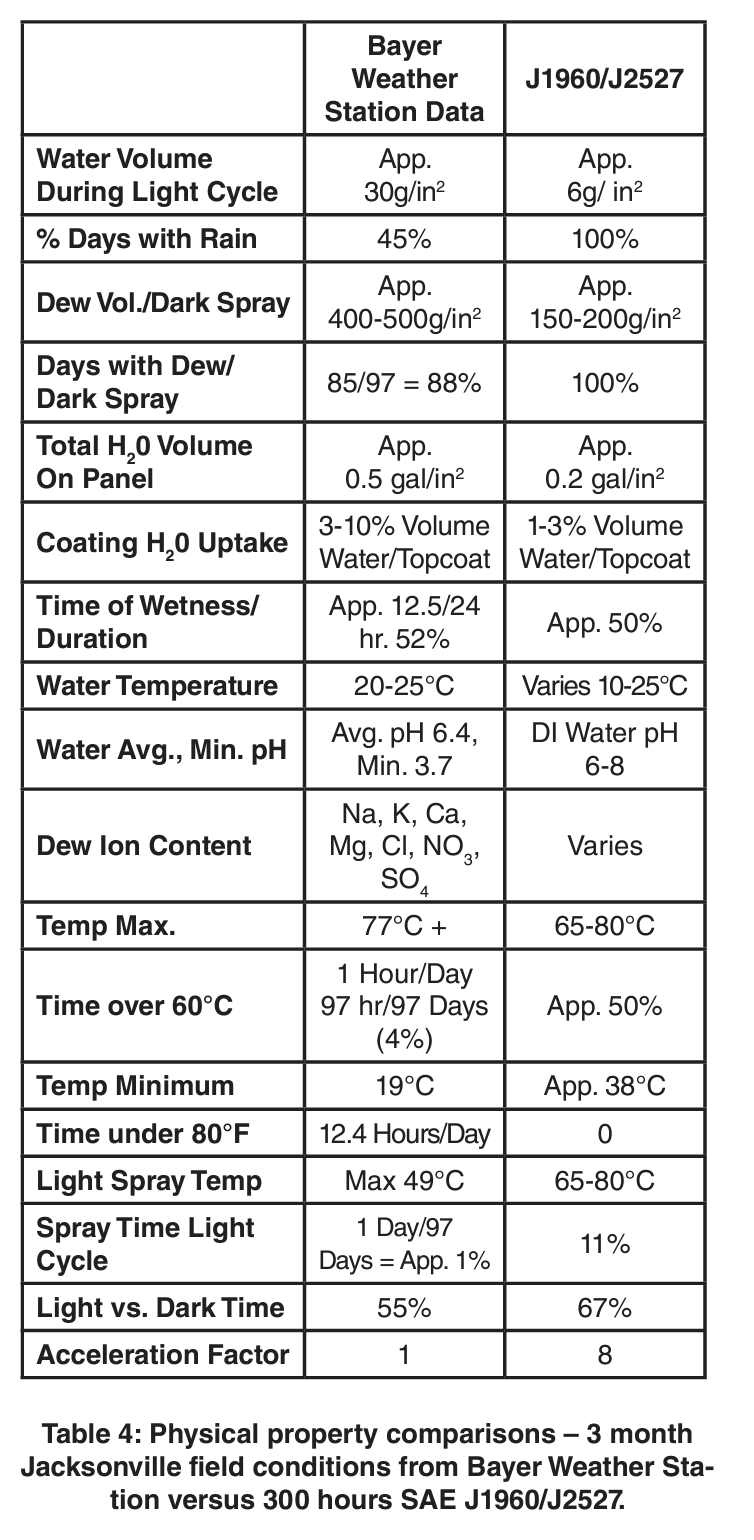
It is worth noting that this condensation exposure is a standard feature of fluorescent UV weathering devices and associated test standards. Figure 5 shows the maximum water uptake possible in a typical automotive coating system versus uptake achieved in SAE J2527/J1960. Additional testing showed that this maximum uptake could be replicated by an extended cycle of water spray in a rotating rack tester and was relatively easy to achieve in a flat array tester. The next series of tests were designed to show how to achieve similar uptake in either tester versus the Florida environment. See Figure 6.
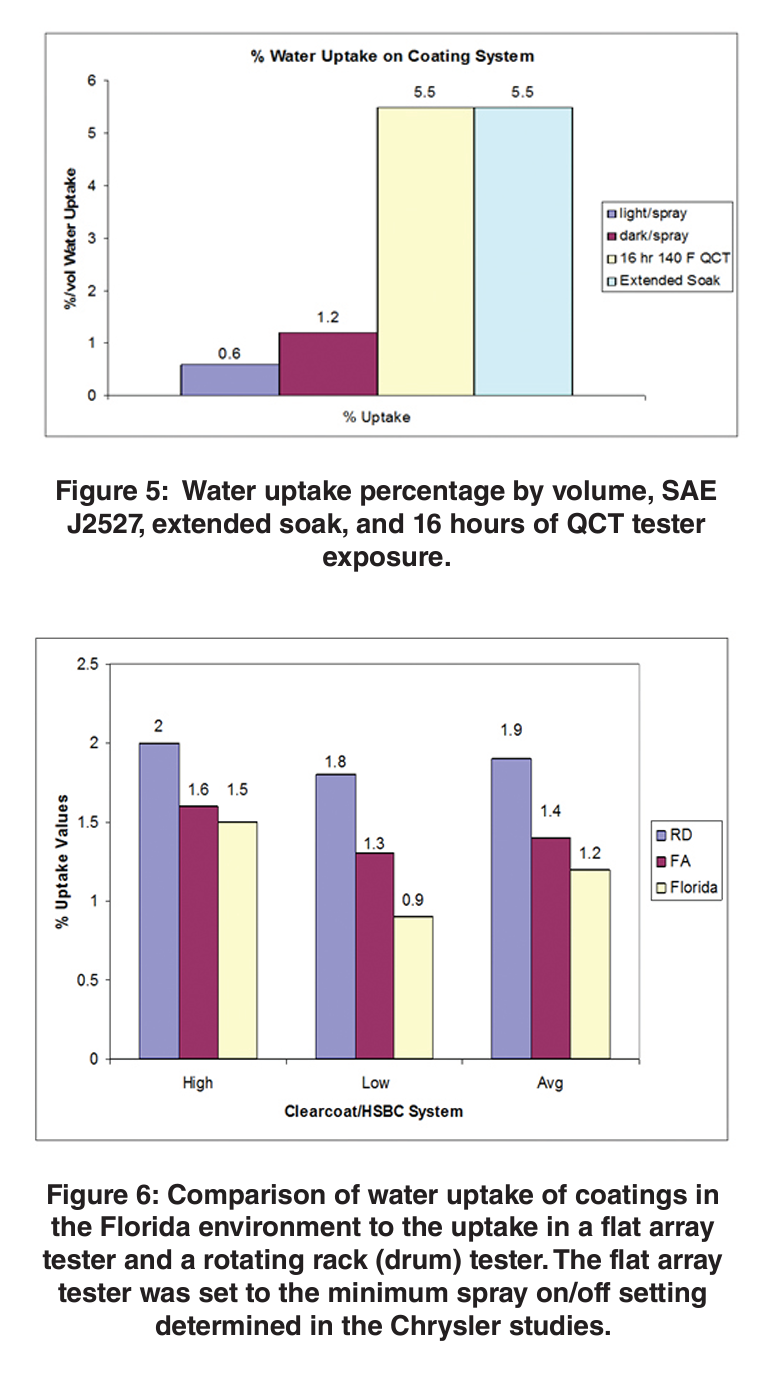
Fixing the Flaws: Ford Leads the Improvements
The research coalition of BASF, Bayer, and Q-Lab needed OEM support and leadership to move weathering testing of automotive coatings beyond the flawed SAE standards. Chrysler, having provided critical leadership to move the industry to performance-based standards, was undergoing organizational changes that prevented active participation in the next phases of research. Ford, having worked to develop an improved optical filter for xenon arc weathering chambers, stepped in to provide leadership.
First on the agenda was taking the moisture research a step further by creating a model that correlated moisture uptake in coatings with weather conditions and applying it to xenon arc weathering chambers. The model would inform the next steps in the program. The goal of this phase of the research was to determine how much moisture the chambers were capable of delivering and then develop test cycles that achieved comparable moisture uptake to panels in Florida.
Measuring water delivery in a flat array tester was straightforward. A special sample tray with measuring cups directly captures water spray. This technique was ineffective in a rotating rack tester however. After trying several methods to measure the amount and uniformity of water delivery in a rotating rack xenon arc tester, the use of a sponge was found effective in both types of chambers, as specified in the new ASTM D7869.
Some of the major conclusions from these studies were the following:
- The spray time per minute needed to be increased in the flat array tester to achieve moisture uptake in coatings similar to Florida test results. Spray time previously had been reduced significantly to achieve results that matched the rotating rack results running the old SAE standards.
- It was possible for a rotating rack to achieve moisture uptake in coatings similar to Florida results. This required a long spray step with no irradiance at the beginning of the cycle.
- A method to calibrate the water spray systems in xenon arc testers needed to be included in future standards for coatings due to the significance of water uptake.
- Use of a standardized sponge was the most effective method to calibrate the water spray system in a xenon arc weathering chamber.
- Non-uniformity of water spray and other factors necessitated specimen repositioning in rotating rack chambers as a requirement in future test standards. Repositioning of specimens in flat array testers was already a requirement in most standards.
- Inclusion of water spray steps with irradiance created unrealistic degradation in coatings and therefore should be avoided.
Ford then supervised a series of round robin tests to create an effective test cycle. Joining the research team for this lengthy phase of the program were Honda, who had independently been doing similar work, Atlas, and Boeing6. The addition of these companies was important in achieving wide industry support for any test standard resulting from this research. Boeing also brought different coatings technologies to the program, broadening the scope beyond the automotive industry.
The specimen set included 106 combinations that included:
- Multiple colors: black, white, blue, red
- Waterborne & solventborne basecoat
- Solventborne clearcoat
- Different layering systems
- Systems with and without stabilizers
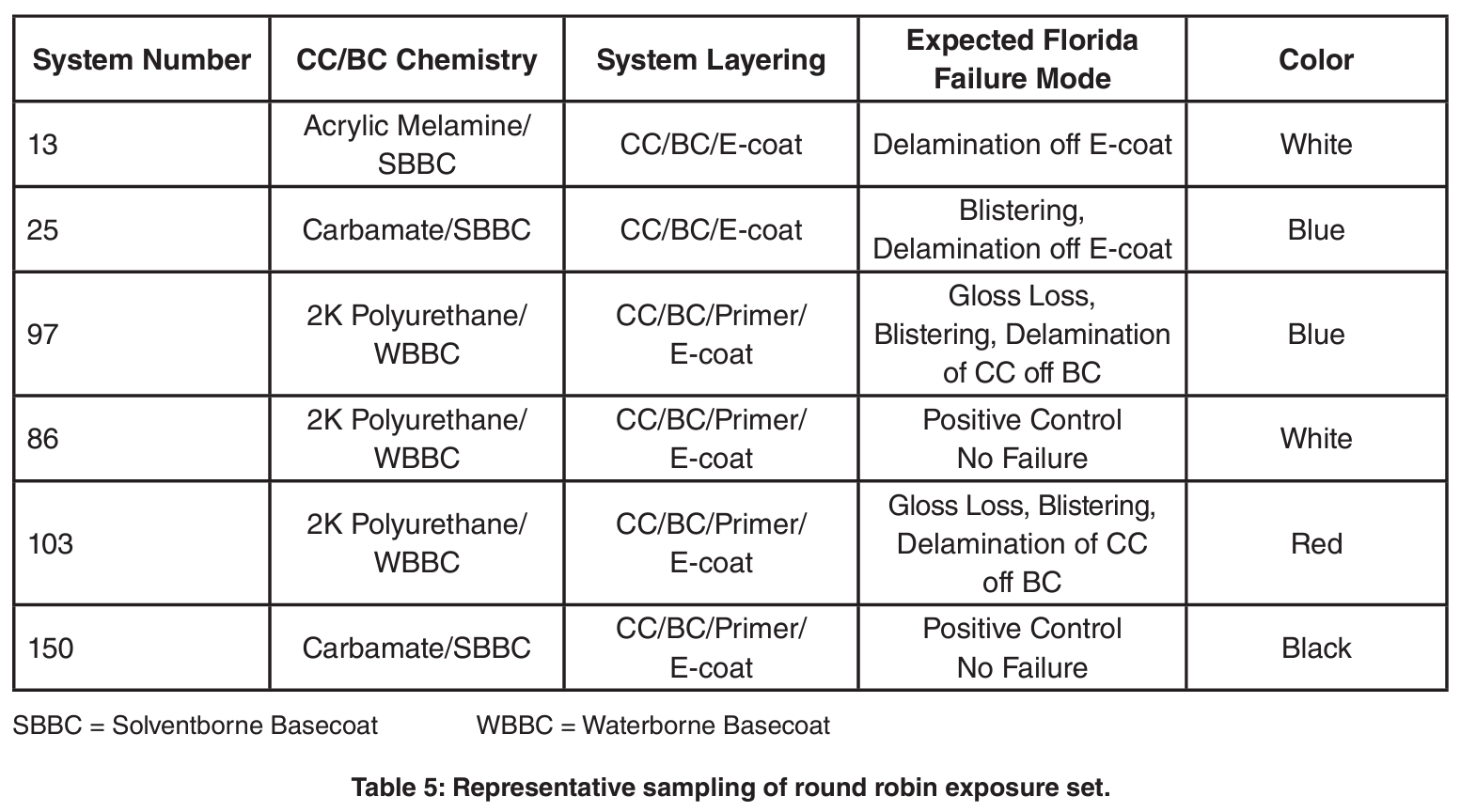
Many of the coatings systems were formulated specifically to reveal certain failure modes. Others were formulated with stabilizers so that no failure mode was expected. The purpose of this design was to evaluate accelerated weathering test cycles for false positive and false negative results. Table 5 shows a representative sample of the specimen set to illustrate this point.
To evaluate these coatings, the researchers employed a mixture of visual and analytical techniques. Color and gloss readings, performed instrumentally, were accompanied by visual evaluations to look for physical defects. As in the earlier Ford studies, PAS-FTIR was used to measure photo-oxidation. To measure the migration of UV absorbers within certain coating systems, ultraviolet microspectroscopy was used. This test required punching out a one-centimeter circular disk from panels and performing a painstaking procedure to isolate the coating film for measurements.
All specimens were exposed at a south Florida test site for a minimum of two years. Automotive panels were returned for evaluations to the same laboratory every 6 months. Aerospace coatings were evaluated for color and gloss every 3 months.
Accelerated tests were performed in Atlas Ci4000 and Ci5000 rotating rack xenon arc test chambers and the flat array Q-SUN Xe-3-HS from Q-Lab. A total of 6 rotating rack and 4 flat array test chambers at multiple sites were used in the studies. In addition, some specimens were tested in a Ci35 according to SAE J1960/J2527. The exposures were timed to achieve a minimum of 3000 kJ/m2 at 340 nm.
The original SAE method had shown acceptable accuracy in anticipating color and gloss loss for many coatings. Flaws in this cycle resulted in its failure to reproduce photo-oxidation, cracking, blistering, and delamination. Consequently, this study largely focused on these areas. As discussed above, the earlier Ford work had identified spectral mismatch between the optical filters commonly used in xenon arc weathering chambers and sunlight as a primary cause of inaccurate reproduction of photo-oxidation during weathering cycles. Also discussed above, an improved optical filter was developed for weathering applications and used in this study.
Figures 7, 8, and 9 show a schematic representation of moisture and irradiance cycles of a typical day in Florida, the old SAE cycle, and the new cycle published in ASTM D7869. This new cycle represented a hybrid of two common approaches used in laboratory weathering cycles. Alternating long periods of wetness and irradiance are common in fluorescent UV testers such as the QUV weathering test chamber because of that technology’s origins as a condensation tester for blistering of coatings. Rapid cycling designed to compress a typical daily exposure into a few hours in a chamber is a common feature of many xenon test cycles, including the original SAE cycle.
In this study, a 12-hour dark step with water spray followed by 12 hours of irradiance without water spray was able to produce blistering and delamination in coatings that exhibited these failure modes after Florida exposure. This result demonstrates the importance of reproducing moisture uptake in the laboratory8. This cycle was not able to reproduce cracking in coatings that experienced this failure mode in the outdoor test. Using an exhaustive, iterative approach, the researchers in these latter Ford studies adjusted the periods of the long spray and irradiance cycles and rapid light/dark/spray/temperature cycling to optimize correlation of all failure modes on all coating types. These experiments lasted several years. The ultimate cycle as published in ASTM D7869 is shown in Table 6.
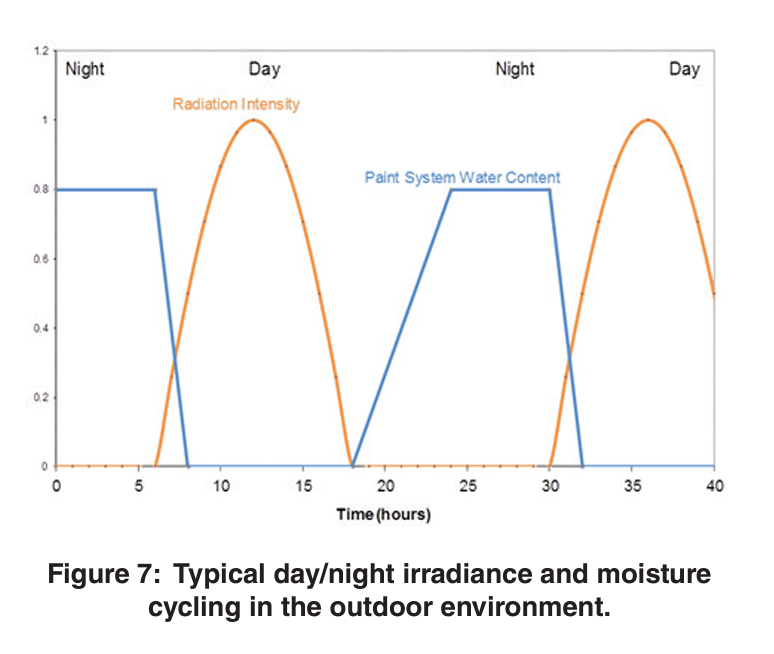
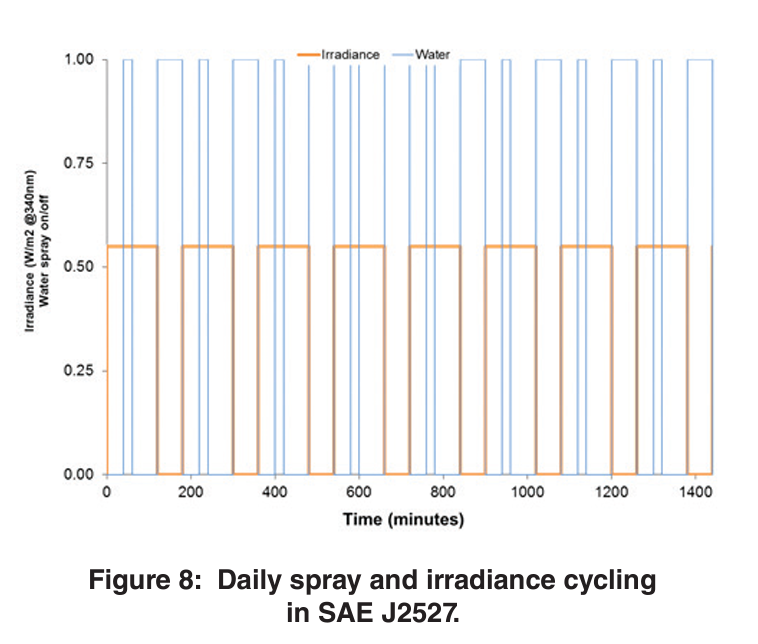
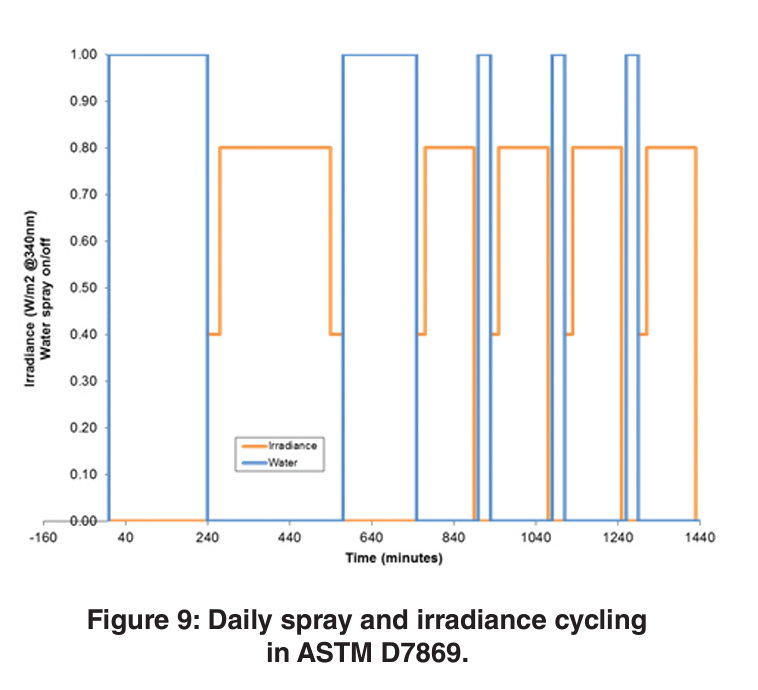
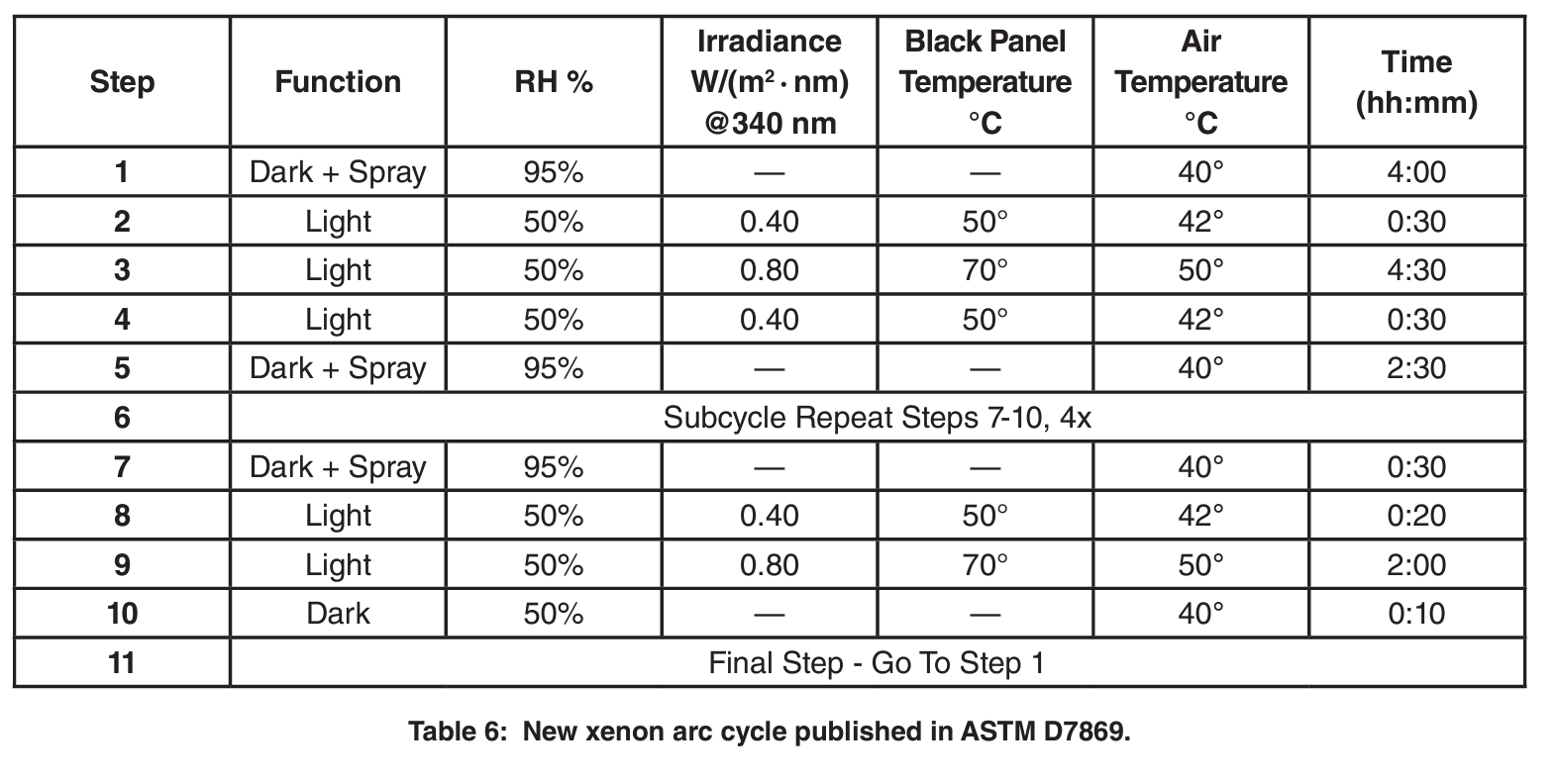
The new cycle showed excellent correlation to south Florida outdoor results for all of the degradation modes examined and all of the coating systems tested. For the first time, a single exposure correctly anticipated outdoor results for color and gloss loss, blistering, cracking, loss of adhesion, and photo-oxidation. One other degradation mode, consumption of UV absorbers, was reasonably well replicated in the new cycle but did not occur at the same rate as chemical degradation.
A very interesting finding was that “frequency of the temperature and wet/dry cycles also scales appropriately with Florida exposure6.” A typical Florida day results in 8.4 kJ of exposure to radiation at 340 nm. The original SAE cycles (J1960/ J2527) results in 3.9 kJ per stress cycle. The new protocol results in 9.9 kJ per stress cycle, much closer to the natural conditions than the SAE cycle. In other words, the new cycle is better than SAE J2527 at overall simulation of the natural weathering factors that degrade coatings.
Not only is the new protocol a better simulation of natural weathering, it’s faster. If the test is based on radiation dosage, the two tests are about the same. On a time basis, however, the new protocol is 40% faster than J2527. This is because the new cycle uses a higher irradiance than the old and has slightly longer overall duration of irradiance than before.
However, the new test does not provide a universal acceleration factor, what’s often referred to by weathering experts as a "magic number." Acceleration factors were calculated in this study. For automotive coatings, they ranged from 8 to 16. In other words, a month of testing with the new protocol was similar to 8 to 16 months outdoors in south Florida. For aerospace coatings, which typically do not have clearcoats, the acceleration factors were much smaller, approximately 3 to 4. For anyone using this protocol with no knowledge of the outdoor performance of their materials, there is significant room for error in assuming an acceleration factor. The need for outdoor testing has yet to be eliminated.
Conclusions
The state of the art of accelerated laboratory weathering has been expanded. For the first time, a single laboratory exposure was able to accurately correlate to an outdoor exposure for both a variety of coating systems and all of their critical failure modes. The new protocol is better and faster than its predecessor.
The technical breakthroughs required to achieve this result included:
- The development of a new optical filter for xenon arc weathering chambers that offers a better match to sunlight.
- Methods to accurately measure outdoor moisture uptake in coatings and moisture delivery in xenon arc weathering devices.
- A novel combining of the strengths of traditional fluorescent UV and xenon arc test cycles. Fluorescent UV tests typically alternate between long duration dark wet cycles and long UV cycles at slightly elevated irradiance compared to maximum sunlight. Xenon tests typically include rapid cycling between wet and dry conditions and run at slightly lower irradiance than maximum sunlight. The new xenon arc protocol includes alternating wet and light cycles at elevated irradiance and rapid cycling to create thermal stresses.
Creation of ASTM D7869 represents an organizational achievement in addition to its advancement of weathering science. It is the culmination of a series of projects that began at the turn of the 21st century involving several companies and dozens of researchers, many of whom were competitors in their respective markets. Old standards had to be replaced by new performance-based documents for an open market to develop, without which innovation would have been hindered.