Road and Paving Sealer
Case Study
Last Updated 2024
Background
Asphalt paving is exposed in all parts of the world under the most extreme conditions. Sealer is applied directly over the top of existing, and partially degraded, asphalt to restore the surface to a new-like condition. The sealer has to adhere to the existing surface and provide weather protection. The current expected durability of pavement sealers is about 3 to 4 years.
Q-Lab reviewed several test methods to determine which might be a good accelerated predictor for the durability of asphalt sealer. This product is coated over driveway and road material to seal out weather effects (Figure 1).
Figure 1: Typical application of pavement sealer
This product is more susceptible to the “non-traditional” effects such as water permeation and freezing, than other materials such as paints and plastics. Paving and sealer failures are cracking, erosion, and fading (Figure 2).
Figure 2: Typical pavement failure
Problem Statement
The manufacturer needed an accelerated test that would accurately predict the long-term exposure of road sealers. Currently the only test that works correctly is a longer duration outdoor test.
There are times when an accelerated test method does not have all the conditions needed to recreate the end-use environment. Traditional laboratory chamber exposures using standard cycles were not severe enough to cause this product to deteriorate in the same manner as was being seen in the field or on outdoor tests in a northern climate. Standard tests do not generally include any freezing steps, or perhaps do not administer enough water to the test specimens.
An accelerated test has to be correct, but it also has to be fast enough to allow multiple modifications to be made to a formula. A good accelerated test allows the specimens to be evaluated under controlled conditions, and can be run at any time of the year.
Study
One accelerated method stood out as a possible solution to this issue a Q-TRAC Solar Concentrator test with a daily soak/freeze/thaw cycle. This test was originally developed for factory-coated hardboard siding and published as ASTM D5722. More recently this test has been successful for testing bituminous roofing materials, so the probability was high that it would also work for road sealers.
Several other test methods were evaluated using the same specimens as a comparison:
Test 1: Accelerated Test ASTM G154 Cycle 7 for 600 hours
Test 2: Accelerated Test SAE J2527 for 1000 hours
Test 3: ASTM G90 Spray 1 for 90 days
Test 4: ASTM G90 Soak Freeze for 90 days
Test 5: ASTM G90 Temp Limited and Spray 2 for 90 days
Test 6: Outdoor Florida for 12 months
Test 7: Outdoor Arizona for 12 months
A set of 3 replicates of 15 different sealers was created for 7 different accelerated weathering tests. One specimen was retained as a file specimen and two were exposed. The specimens were periodically evaluated for deterioration and photographed. For baseline reference we used the specimens exposed for 21 months on a horizontal rack in Wisconsin (Figure 3).
Figure 3: Outdoor exposure in Wisconsin
Results
Laboratory testing did not produce any significant changes in the specimens (Figure 5). The conditions were not harsh enough to initiate failures or produce the degradation seen in the Wisconsin exposures. Learning from these results, we could suggest other laboratory tests that would be better and faster, but this study only looked at standard exposures.
Figure 5: Laboratory test exposure results, showing little to no change
Of the outdoor tests, Florida showed some of the same degradation but not enough to allow for the differentiation needed. There was no clear deterioration in many of the specimens exposed in the Arizona tests. The amount of water likely reduced the Arizona test, while the lack of freezing slowed down the Florida test. The slower rate of deterioration in the Florida test - which normally is faster than northern exposures - rules this out as a suitable test.
All of the solar concentrator tests were much better at producing defects and matched well the outdoor Wisconsin exposures . The specimens in the Q-TRAC Soak/Freeze/Thaw (SFT) test was the only test that showed the any discernible differentiation of results (Figure 5 and Table 1). We were able to group all the specimens into three broad classes: Best, Median and Worst. The Q-TRAC SFT test correctly identified the three best performers of the outdoor test.
Figure 5: Photographic comparison of Q-TRAC S/F/T to outdoor Wisconsin
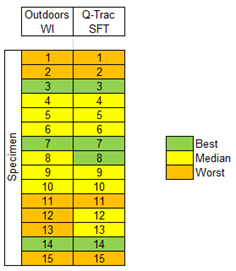
Table 1. Qualitative comparison of Q-TRAC S/F/T to outdoor Wisconsin
Not all Q-TRAC cycles were as effective at differentiating between performance. The least amount of degradation was observed in the temperature-controlled test, probably as a result of the specimens not reaching the temperatures found on a black specimen, and the spray 1 (daytime) cycle was most likely deficient in allowing enough water to penetrate into the specimen.
Conclusion
The best exposure test in our study that correctly recreated the relative rate and performance of the real time outdoor test in Wisconsin within the test time period was the Q-TRAC Soak/Freeze/Thaw test. A 90-day exposure on the solar concentrator appears to be able to accurately predict the performance of a 2-year exposure.
Note
The ASTM D5722 method uses the Q-TRAC solar concentrator, where the specimens are exposed during the day to the Spray 1 (daytime) cycle. At the end of the day the specimens are removed from the exposure location, and placed in a water bath at ambient temperature for one hour. The specimens are moved to a freezer at 0 °C overnight, thawed out in the morning then returned for solar concentrator exposure.
References
- Rust-Oleum online catalog of sealer products
- Brett Neal, PaveMan Pro (Sealcoating)
- Sealmaster online photos